UCSF Bayfront Medical Building
The project is a 5-story medical building including clinics, urgent care, and an ambulatory surgery center located on the east side of the UCSF campus. The over 180,000 SF project set a goal of achieving LEED Gold. In parallel with the life-cycle embodied carbon reduction credit, the Bayfront design exhibits operational carbon reductions through efficient envelope design and efficient systems, including solar hot water panels to reduce water heating loads.
Executive Summary
The project team conducted a detailed embodied carbon analysis to identify opportunities for reductions early in the design process. Through close collaboration with Central Concrete, the team was able to procure low-carbon concrete mixes using SCMs and CarbonCure technology to achieve substantial carbon savings. This effort, alongside additional reductions from structural steel procurement, resulted in an estimated 36% reduction in embodied carbon for the project (LEED scope, structure and enclosure, A-C) and a carbon use intensity of 391 kgCO2e/m2.
Design started in 2020 with doors opening to the first patient in 2024.
LCA Results
The project aims for a 10% whole-building embodied carbon reduction through the use of low-carbon concrete.
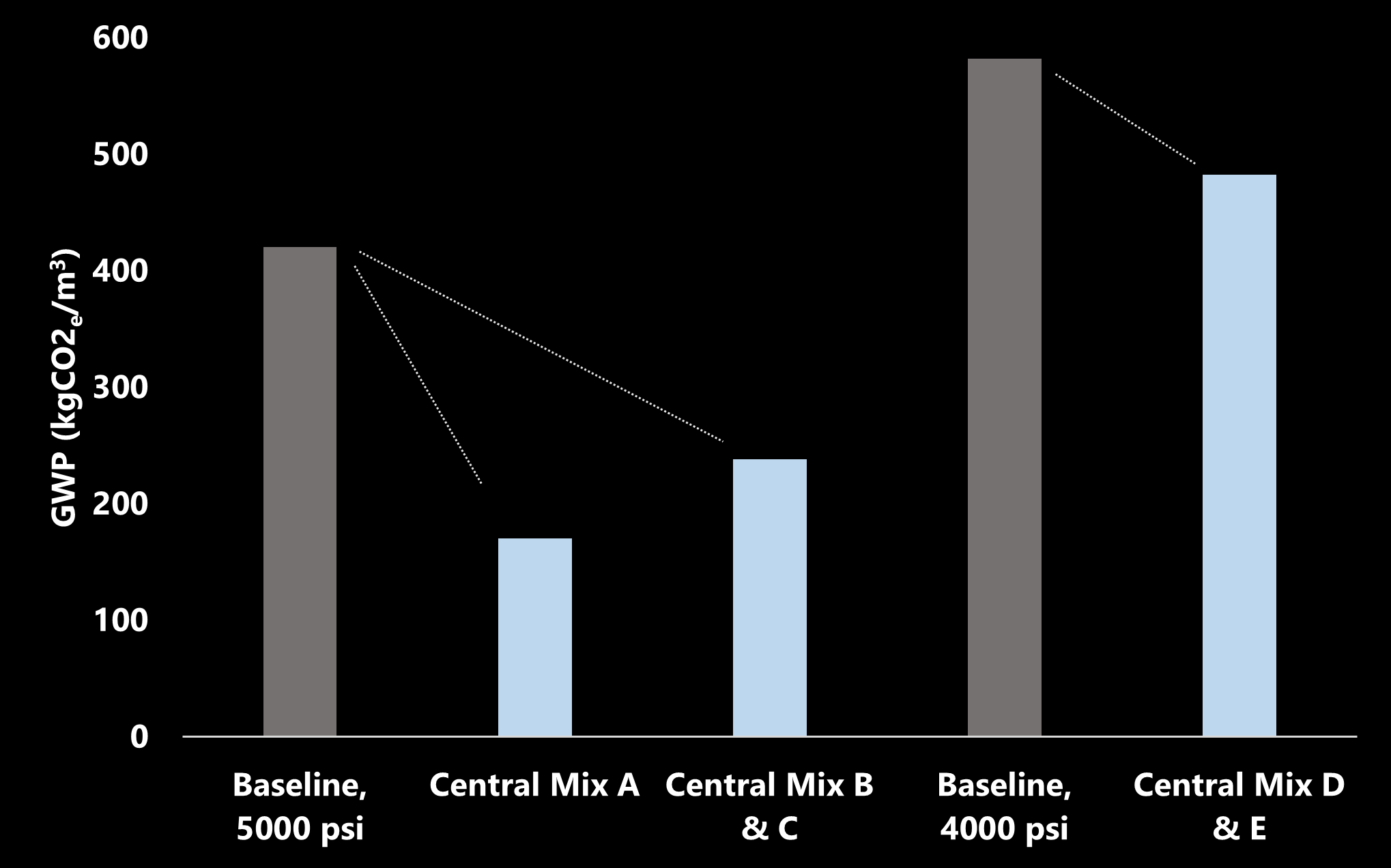
Figure 1. Bar chart compares global warming potential intensity in kg-CO2e per cubic meter of project concrete mix designs to the industry average baseline. The 5000psi mix designs are determined to have a 43-60% reduction and the 4000psi mix design has a 17% reduction.
Central Concrete primarily used supplementary cementitious materials (SCMs) to replace Portland cement to achieve the carbon savings. Additionally, CarbonCure technology, which injects CO2 gas into the mix, was used to further reduce embodied carbon by 3-5%. Custom mix designs were developed for foundation, columns, walls, and slabs. The greatest percent reduction was possible in the foundation, where specified 56-day strength and high cement replacement wouldn’t impact schedule. The greatest total reduction in carbon was from the slabs, which contributed over half of project emissions in the baseline model.
Reduction Visualizer
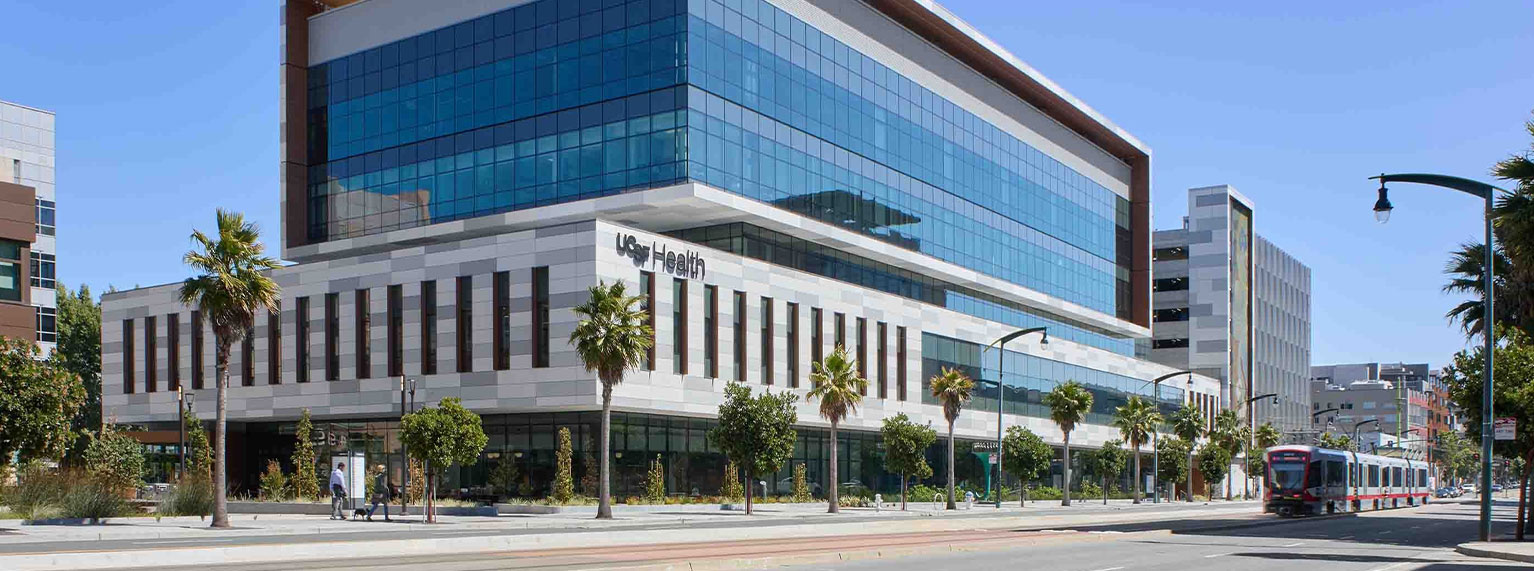
Figure 2. Exterior photo of the finished UCSF medical building.
Alongside low-carbon concrete procurement, further GWP reductions were generated through additional design decisions (Figure 2).
- Procurement of vacuum-insulated, low-e glazing resulted in lower GWP and enhanced energy performance.
- Low-carbon steel was procured from Gerdau’s Midlothian Steel Mill.
- Materials were sourced from the closest manufacturers where possible to reduce transportation emissions (A4).
Motivation and Goals
Bayfront set out to go above and beyond what was required of them, setting an example to the UC community and other medical developments.
Embodied carbon targets stem from pursuing the LEEDv4 Building Life-Cycle Impact Reduction credit but also stretches well beyond the LEED v4 thresholds by achieving an estimated 36% embodied carbon reduction.
UCSF aims to meet the decarbonization goal of 90% reduction by 2045. Bayfront has been the first in a series of projects that has incorporated low-carbon concrete and embodied carbon reduction measures. Creating precedent for concrete carbon reduction has had—and will have into the future—significant impact on Scope 3 emissions from new construction.
Supply Chain of Material
Where does low carbon concrete come from?
Low-carbon concrete is just like any other concrete—it’s just designed with optimized cement content. Local ready-mix suppliers and EPD availability can be determined on EC3, a free online repository of EPDs. Identifying potential local partners can be useful as well as determining reasonable goals.
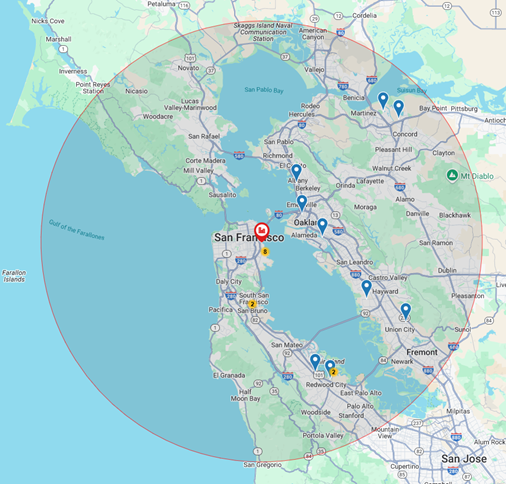
Figure 3. Bay Area Map of Concrete Ready-Mix Suppliers
In Figure 3. the map shows the location of Bay Area concrete ready-mix suppliers who provide environmental product declarations (EPDs) for their concrete mix designs are mostly located in the East Bay. Seven out of nine suppliers are in Alameda and Contra Costa Counties. The remaining two suppliers are in San Mateo County.
Constructability Considerations
Construction (A5): High SCM mixes can take longer to reach full strength. Foundations, columns, and walls won’t see design loads for a long time, but floors may need shoring removed and less flexibility. Coordinate mix designs with the GC to work with the schedule.
Roadblocks and Challenges
Education remains one of the primary challenges on embodied carbon reduction, a topic still relatively new to the building industry. By working with trade partners, such as contractors and material suppliers, we can better understand supply chains to limit waste and inefficiency while reducing embodied carbon.
Top Ways to Reduce Concrete’s Carbon Footprint
- Communicate carbon reduction goals: The team can work toward setting achievable targets. A “carbon conference” between owner, architect, structural engineer, contractor, and relevant suppliers can be valuable to align vision and expectations.
- Optimize concrete design: Each mix is different. A weighted average approach should be used to allow flexibility to meet sustainability goals within the control of the GC. The NRMCA Carbon Tool can be used to set a “carbon budget.”
- Don’t limit ingredients: Overly restrictive concrete specifications can limit the supplier’s ability to optimize mix designs. Limits such as minimum cement content, maximum water-cement ratio, maximum supplementary cementitious materials (SCMs), and exclusion of blended cements like Type IL portland limestone cement (PLC) can limit project potential. Working with the structural engineer to use performance specifications can remove major barriers.
Design Process (Low Carbon vs Usual)
- Schematic Design: Sustainability targets established early in design stage, ensuring that embodied carbon reductions were prioritized throughout the project.
- Design Development: Life Cycle Analysis conducted at 50% and 100% DD in order to identify opportunities for reductions through materials procurement.
- Construction Documentation: Performance-based specifications document low-carbon mix designs.
- Construction Administration: Quality control testing practices by the GC. According to NRMCA, poor testing practices could drive up GWP by 10% or more.
Lessons Learned
- Meaningful embodied carbon reduction is possible on every project. With critical communication of project sustainability goals and collaboration with the general contractor, structural engineer, and ready-mix supplier, this meaningful impact can be done at no cost premium.
- Early engagement from project ownership can build confidence with the design and contractor team to talk about embodied carbon.
- Since Bayview, UCSF has implemented low carbon concrete on Hellen Diller Hospital and the Bakar Research Administration Building. Setting up standards for specifications, including global warming potential performance and removing unnecessary prescriptive language, can lead to positive precedent and a domino effect of carbon savings.
Development Team
Architect: Stantec
Contractor: Clark Construction
Structural Engineer: Rutherford + Chekene
Sustainability: Stantec