UCSF Helen Diller Hospital
The project is a 15-story hospital located in Parnassus Heights. The 880,000 SF project set a goal of achieving a 10-20% reduction in embodied carbon over a typical concrete structure through its use of low carbon concrete.
Executive Summary
Success on the Bayfront Medical Building using low-carbon concrete, UCSF wanted to employ similar strategies on the Helen Diller Hospital. Project location on a steep hillside in high seismic zone led to lightweight concrete filled composite deck and steel framing keep weight and seismic loads to a minimum. Given the quantity of concrete in these solutions, the project team identified low carbon concrete as an important strategy to reduce embodied carbon. Integrated project delivery (IPD) and early communication built trust on the team, including close collaboration between Webcore Concrete and Central Concrete, to test and develop multiple concrete mixes that went beyond OSHPD limits and serve to meet cost, schedule, and sustainability for a variety of ambient (winter/summer) conditions.
Design started in 2020 with the first patient day slated in 2030.
LCA Results
The project aims for a 10% whole-building embodied carbon reduction through the use of low-carbon concrete (Figure 1). The Alternative Means of Compliance (AMC) concrete mixes outlined in the project go beyond OSHPD constraints. This was necessary to achieve embodied carbon goals. Concrete mixes were sent for AMC approval for foundation, walls, slabs and lightweight concrete on metal deck (Targeting 70% SCMs and 56-day strength gain).
The bar chart in Figure 1. compares the embodied carbon of four different concrete mixes. The low-carbon concrete at Helen Diller Hospital used an Alternative Means of Compliance concrete mix that reduced that whole-building embodied carbon by 10%.
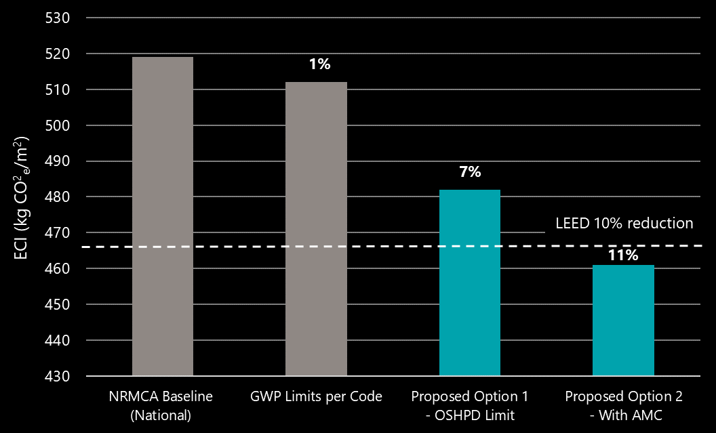
Figure 1: Baseline: NRMCA Concrete Benchmarks; Proposed: AMC Optimized concrete mixes.
In order to meet embodied carbon reductions, its recommended to follow a Low Carbon Concrete Checklist:- Contractor and supplier engagement
- Performance-based specifications
- Cement replacement
- Later day strength (e.g. 56-day)
- Aggregate: High strength (NWC); Natural (LWC)
- Portland limestone cement
- Carbon mineralization
Reduction Visualizer
Figure 2. This exterior architectural rendering of Helen Diller Hospital shows the metal decks and pile caps
In the photo above, you can see the following emboddied carbon reductions:
- Topping over metal deck was able to reach up to 70% SCM content and natural lightweight aggregates
- Interior and retaining walls were also submitted for AMC approval
- Majority of pile caps were allowed a 56 day curing time with no schedule impacts
Motivation and Goals
This project set out to go above and beyond what was required of them and even went beyond code constraints, overcoming obstacles and setting an example to the UC community and other medical developments.
- Embodied carbon targets stem from pursuing the LEEDv4 Building Life-Cycle Impact Reduction credit but also stretches beyond LEED with a 10-20% reduction goal to align with more rigorous ILFI targets.
- Embodied carbon reductions were part of their UC Scope 3 Emissions strategy in their technical performance criteria, doubling down on goals.
- As an institution prioritizing global health, the team recognized that combatting climate change is paramount to global health, therefore reducing carbon was critical to this aim.
- As a UC project, this had high potential to pave the way for low-carbon design as a model project for healthcare projects in the future.
Supply Chain of Material
Where do carbon impacts of low carbon concrete come from?
They come from Manufacturing (A1-A3): The most carbon-intensive component in concrete production. SCMs (e.g. slag, fly ash) replace traditional Portland cement.
Lightweight concrete requires lighter aggregate. Commonly this aggregate is manufactured at high temperatures as well as more cement needed to meet strength. Natural aggregates, such as pumice, reduce embodied carbon on LW mixes.
Then in Construction (A5): High SCM mixes usually take more time to reach full strength gain. The team coordinated mix designs with the critical path to ensure no project delays.
Roadblocks and Challenges
1. The primary hurdle of the hospital project’s ambitious low-carbon concrete goals were the limitations set by OSHPD (the office that regulates California construction of healthcare facilities).
2. Key OSHPD Limitations on Concrete:
- Max 50% SCMs (low-carbon concrete would strive for high SCM content)
- Max 28-day curing time (high SCM mixes often require longer curing times)
3. The team had to go through an AMC process to allow low-carbon mixes to be introduced to the project and thereby meet embodied carbon goals.
4. These limitations are described in concrete building code, but limited to concrete exposed to freeze thaw with continual exposure to water and deicing chemicals (F3)—a condition that does not apply for most California projects.
5. Central Concrete (concrete supplier) was critical for AMC success, suppling representative mixes, and an abundance of historic test data to demonstrate performance requirements of alternative mixes.
6. Allowed mixes, including for the metal deck topping, were allowed to reach 70% SCMs. There was no perceived increased to cost.
7. A majority of the pile caps were allowed a 56-day curing time. This was worked into the schedule ahead of time but did not cause delays as the steel columns did not need to be erected until much later.
Design Process (Low Carbon vs Usual)
- Concept: Contractor brought on early to provide input on constructability through integrated project delivery (IPD)
- Schematic Design and Design Development: AMC concrete mix designs developed and reviewed with Central Concrete and OSHPD
- Construction Documentation: Performance-based specifications document low-carbon mix designs
- Construction Administration: Pile caps were the first to be scheduled with longer curing time. No impact to schedule as steel columns would not be erected immediately.
Lessons Learned
- We are not constrained by what’s required by code.
- Allowances for low-carbon concrete mixes that prescriptively did not align with OSHPD code were conceded upon after discussion and agreements with code officials.
- Embodied carbon reduction is possible on every project. While not as visually evident as mass timber or adaptive reuse projects, the reductions are impactful and viable—even with significant code or cost constraints.
- Having the contractor on early enabled success. Investment of time and effort to develop, plan, and review concrete mixes is key.
Development Team
Architect: HDR, Herzog & de Meuron
Contractor: Herrero Boldt Webcor
Structural Engineer: Nabih Youssef Associates
Sustainability: Arup (LCA), HDR, Mazzetti